It takes no less than ten steps to manufacture EGIDE bicycle, ski or riding helmets, in leather or technical materials. All these steps are carried out by hand, in Brie-Comte-Robert and Cholet.
Manufacturing
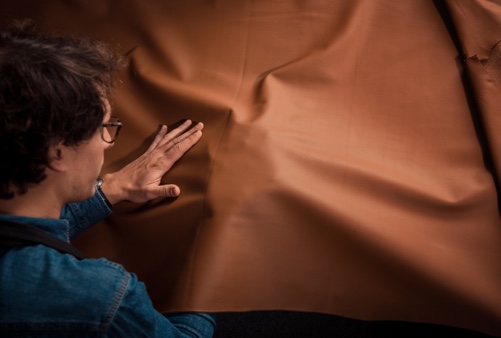
1
Leather selection and processing
The full-grain leathers used for EGIDE helmets are selected from the most renowned tanneries.
They are then mass-treated, guaranteeing unfailing resistance to rain, UV and surface aggression.
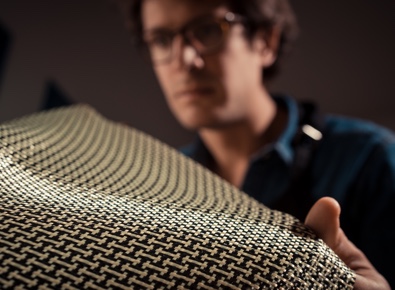
2
Carbon / Fiberglass: selection and treatment
For technical materials, EGIDE has chosen carbon and fiberglass. Used in the aeronautics industry for high-performance technical parts, these materials guarantee helmet strength, lightness and safety. Their surface is then coated with an anti-scratch varnish.
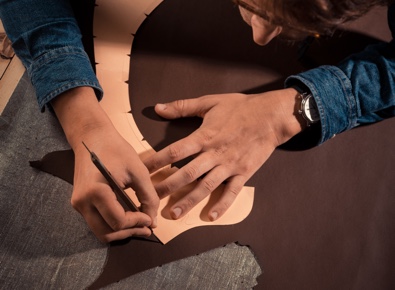
3
Cut
leathers
The next stage in the manufacturing process: the leathers are cut by hand, to ensure that the leather craftsman is able to locate and select the parts without imperfections.
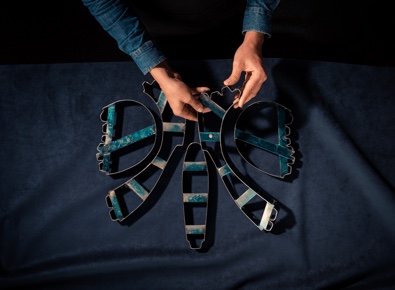
4
Carbon / Fiberglass: The cut
As with leather, technical materials are cut by hand, this time with a die, according to rigorous draping plans. The craftsman's eye guarantees that the selected pieces are flawless.
5
Leather sewing
Joints and topstitching are made by hand, using a special thread selected for its high resistance to rain, UV and surface abrasion.
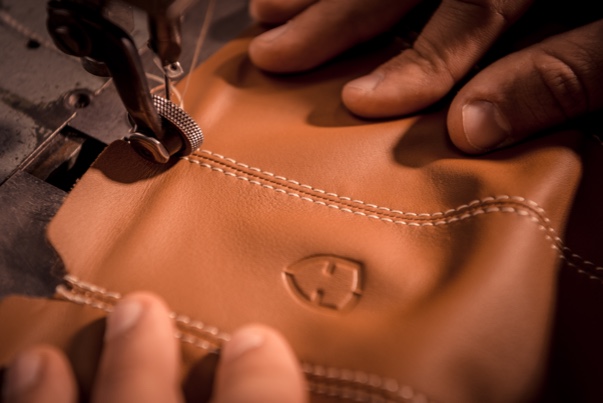
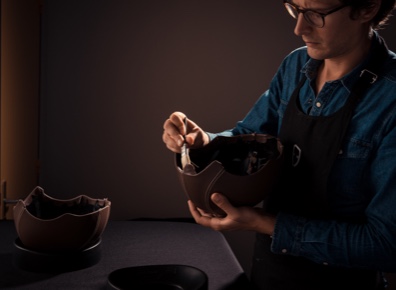
6
Gluing and sheathing
Once the surfaces have been prepared, the skullcap is glued and the leather is applied to the skullcap. An inspection is necessary after the drying time.
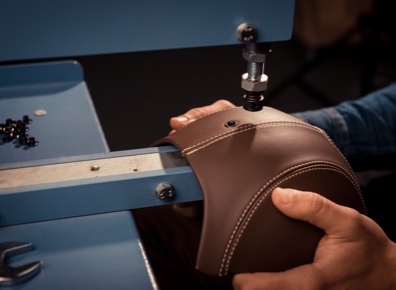
7
Assembly
The components added at this stage are checked and weighed one by one. The chinstrap and ventilation eyelets are then crimped, the protective foam glued, and the visor fitted.
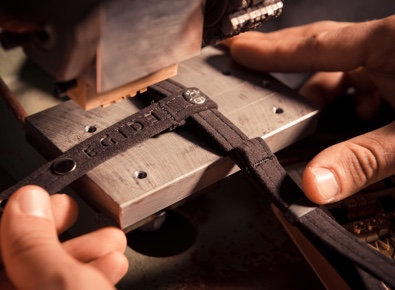
8
Marking
Hot-stamping of the EGIDE logo on the helmet and chinstrap completes the meticulous finish.
9
Certification
and compliance monitoring
Once manufactured, each helmet is subject to European standards:
These tests are carried out at extreme temperatures (from -20 to +50°). Random certification follow-up tests are carried out in collaboration with an accredited French laboratory.
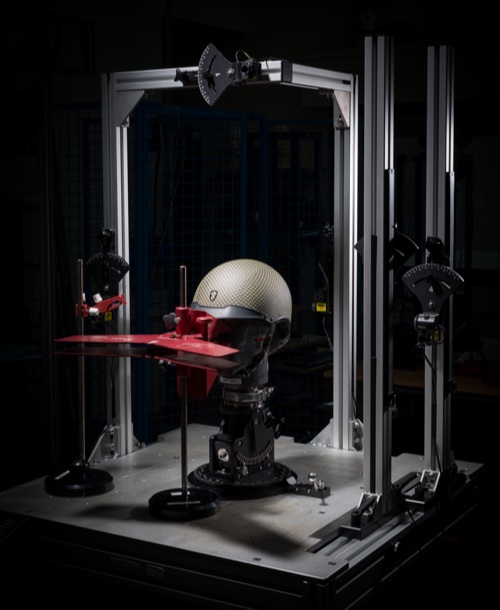
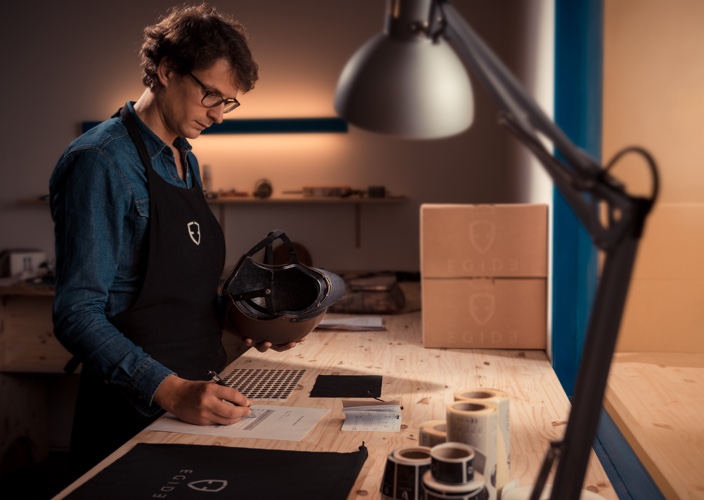
10
Control / Shipping
Final step: each helmet is inspected one last time. All helmets are numbered for traceability. Before being carefully packed and delivered with the owner's manual in a protective cloth bag.